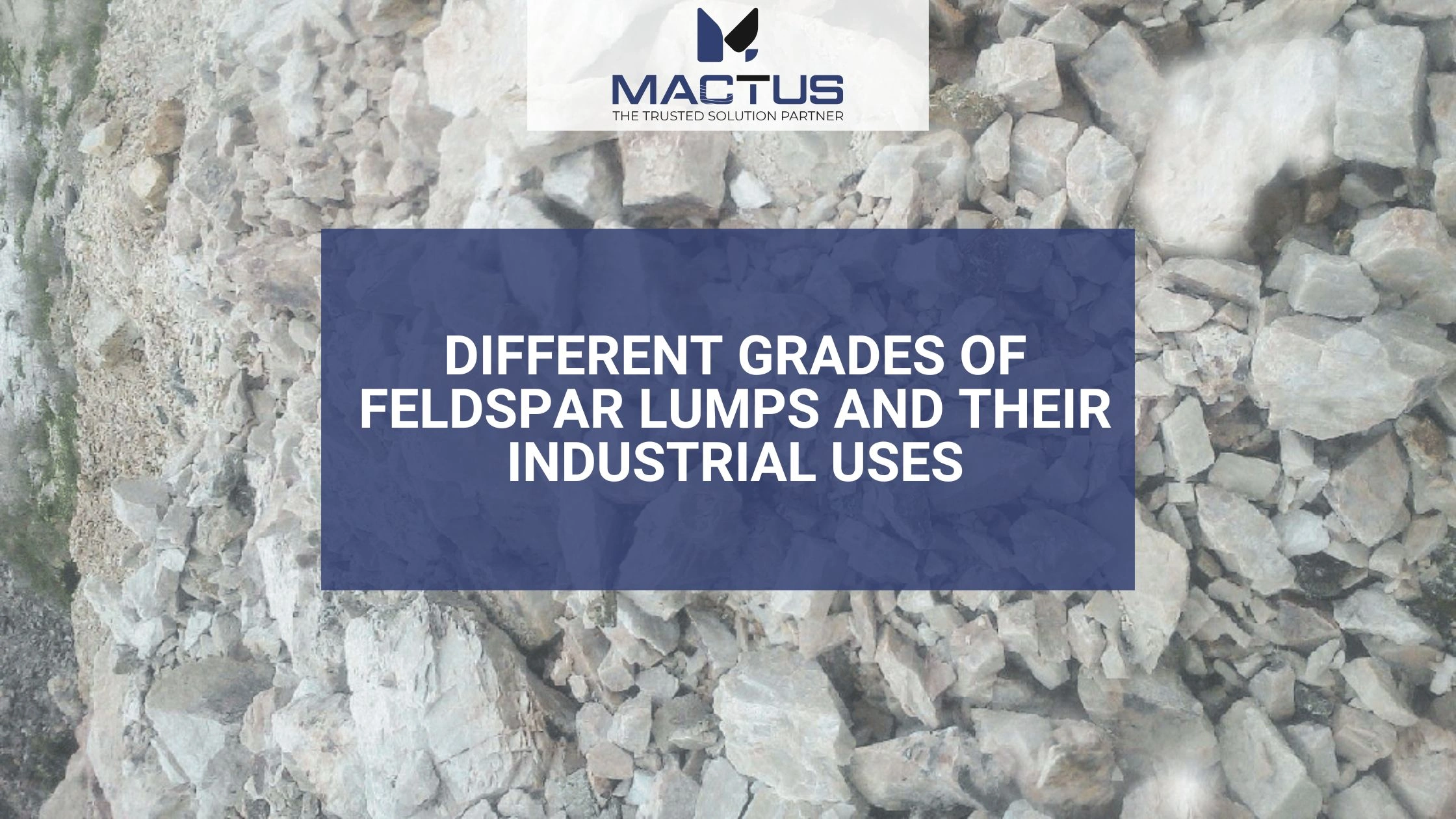
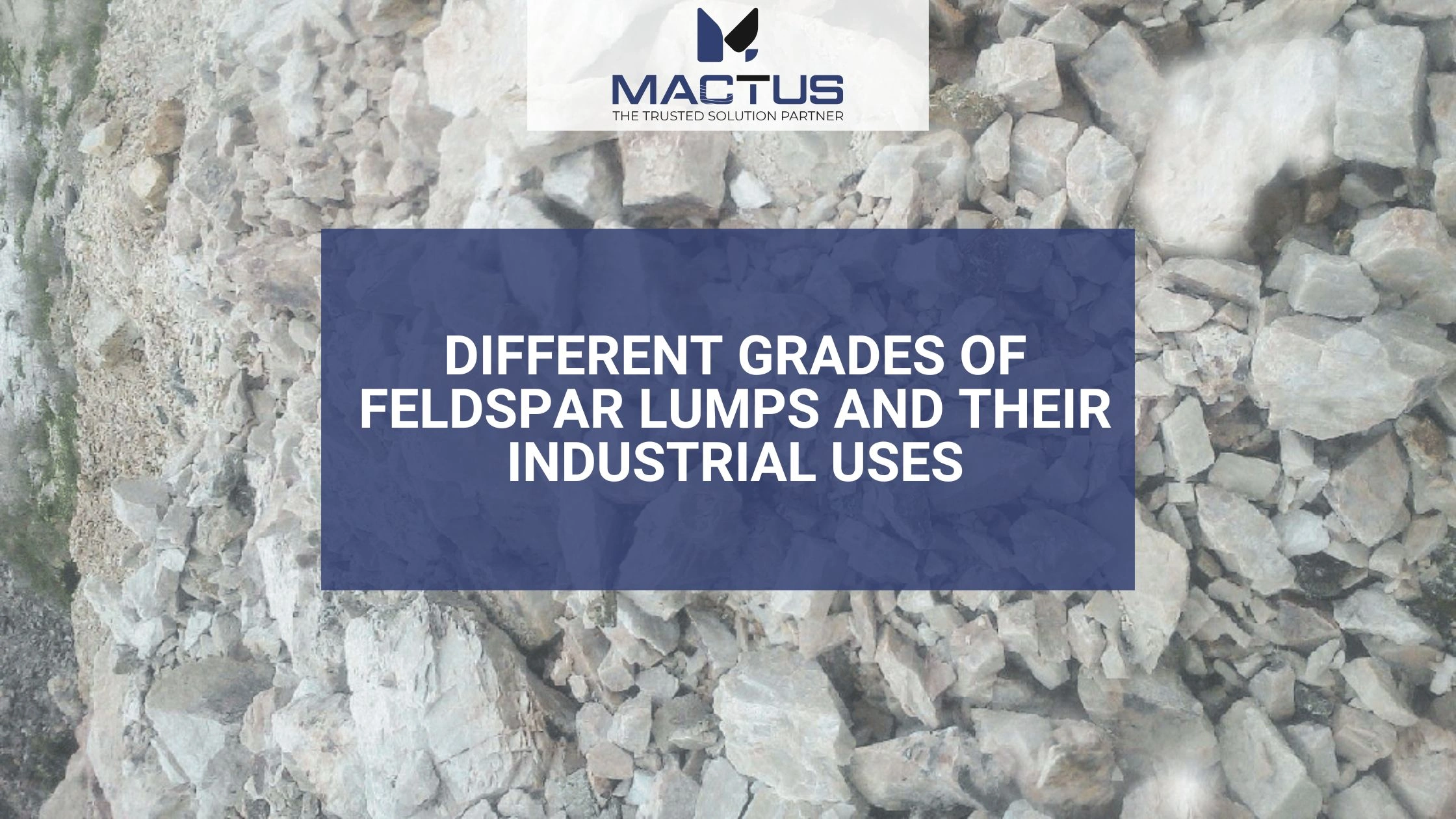
Connect With Our Team
Among the industrial minerals, feldspar is one important constituent of various industries, particularly in ceramics and glassmaking. There exist broadly two types: the potash feldspars rich in potassium and the soda feldspars rich in sodium. While there are a lot of similarities between them, certain differences in their inherent properties make them suitable for specific uses. This blog reviews the extraction, refining, and processing of feldspar with regard to its use in industries, discussing the main differences between potash and soda feldspar.
This is the most common method applied for Feldspar extraction due to its efficiency in reaching near-surface deposits. Large amounts of material are removed using heavy machinery that includes excavators and trucks. The overburden, or surface material above the deposit, is removed, to expose the Feldspar-bearing rocks. These rocks are drilled and blasted in order to break them down into manageable pieces for transportation.
Where the deposit is located far from the surface, underground mining, though seldom applied, is resorted to. It involves the sinking of shafts or tunnels to reach the mineral. It is generally more expensive and environmentally challenging but sometimes necessary to reach high-quality deposits.
After mining, the Feldspar rocks undergo a primary process -crashing. This is the initial step toward the downward reduction of big trunks of mined material into manageable pieces. The jaw and impact crushers do the job here, reducing the Feldspar to sizes that may enter the subsequent stage of processing.
The Feldspar, after reduction, is pulverized into powder to a stage when it can be industrially used. Grinding is done by grinding mills such as ball mills and rod mills. The reduction in the size of the particles is very important because different industries need feldspar in different sizes. For example, ceramics industries usually need ground feldspar to a fine size for smoothness in the end product, whereas on the other hand, glassmakers industry might need coarser grains.
After the feldspar is ground, various separation techniques are applied to separate the potash feldspar from the soda feldspar.
Separation of magnetic iron-bearing minerals of Feldspar. The ore must pass the magnetic separators that attract the iron particles and retain it ensuring that the remaining material is free of metallic impurities.
The separation of Feldspar from quartz and mica is done by flotation. In the process, several chemicals, referred to as flotation agents, are mixed with ground Feldspar in a water suspension. The agents influence the action of specific minerals to cling to the air bubbles and float out of the water, to be skimmed off resulting in high-purity Feldspar.
Screening of ground material separates the fines from the coarser particles to achieve more uniform particle sizes to proceed with processing.
The Feldspar requires separation from impurities, which could comprise quartz, mica, iron oxides, and others, for high purity. This step is extremely crucial, particularly in applications such as ceramics and electronics, wherein traces of impurities will affect the finished product.
After separation, the feldspar types undergo specific refining processes to improve their purity. Refining for potash feldspar and soda feldspar involves different techniques, tailored to each type’s chemical and physical properties.
Potash feldspar is more often found to be more impure, particularly with iron. An iron removal may be accomplished by magnetic separation, often followed by flotation in order to produce a high-purity potash feldspar. This type of feldspar is often used in the ceramics due to its higher melting temperature and hardness which adds resistance to products.
Because soda feldspar is usually found in a much purer form than potash feldspar, it requires less refining. Floatation is used to remove any remaining impurities from the soda feldspar. As it melts at a lower temperature than potash feldspar, this type of feldspar is very suitable for use in the manufacture of glass.
After separation, Feldspar is washed to remove any trace amount of impurities or dust. It involves the use of hydrocyclones, which, at high speed, spin the slurry; these separate fine particles from water. The cleaned Feldspar is dewatered into filtration screens in preparation for drying.
Further refinement of the feldspar leads to its processing into an industrial specification product. This refined feldspar is often dried in order to remove moisture and further milled down to desired particle sizes. Sometimes, it may also be blended with other minerals to suit particular customer requirements.
This stage is very critical since the quality control of feldspar needs to meet strict specifications for application industries. Tests to be carried out on particle size distribution, purity, and chemical composition show that this is a high-quality feldspar. Samples are drawn from different batches with the view of ensuring consistency throughout the whole production chain.
After the feldspar has passed this stage of quality control, it becomes ready for packaging and distribution. The feldspar powder is housed in large sacks or containers that may facilitate bulk transportation of the product. There might also be small bagging, depending on customer needs.
After extraction, feldspar is forwarded to glass manufacturers, ceramic producers, and enamel plants for use as raw material in the manufacture of a gamut of products.
While both types of feldspar have a close resemblance with each other, there are some basic differences between properties, processing, and industrial applications of potash feldspar and soda feldspar:
Potash feldspar has higher potassium contents.
Whereas, soda feldspar contains a bit higher sodium content.
Potash feldspar has a higher melting point, making it more suitable for applications that require high heat resistance such as ceramics and porcelain.
Soda feldspar, with its lower melting point, is used more often in glassmaking.
Potash feldspar requires more heavy refinement to take away impurities. Iron impurities are critical to remove.
Soda feldspar is much pure in its raw state removing some of the same refinements.
It finds application in ceramics and glassmaking, also in small quantities as a flux in other industries.
Employed in applications of glass and ceramics, along with glazes, where lower melting is necessary.
Mining, refining, and processing entail very vital stages important in the industrial utilization of this versatile mineral. Each stage utilizes refined techniques specific to each kind in the chain from extraction to the actual refinement of high-quality potash and soda feldspar, and all are crucial to the final product to meet industrial standards and customer expectations.
Presently, feldspar has great applications in ceramics, glass, and construction and, therefore, remains one of the primary raw materials for the production of these materials. Mactus Mineral ranks among the top suppliers with superior quality potash and soda feldspar. These value-added products are produced in conformity with strict quality control to ensure repetitively top performance in industrial applications. With Mactus, one can be sure of supply reliability and quality, and thus, it provides the power of innovation and quality to the manufacturing processes.
Whatsapp Chatx
Hi! Click one of our representatives below to chat on WhatsApp or send us email to [email protected] [email protected]
![]() |
Mr. Vivek Rajpara +91 75750 53447 |
![]() |
Mr. Nikunj Vadaliya +91 98240 66283 |